Specification
Main Parameters | U8519 | U8523 | U8537 | |
Voltage(VDC) | 48 | 48 | 48 | |
Rated Output(W) | 380.42 | 518.76 | 704.78 | |
Rated torque(Nm) | 1.21 | 1.65 | 2.69 | |
Instant Max Torque(Nm) | 3.17 | 4.45 | 6 | |
Rated Current(Arms) | 10 | 14 | 17 | |
Instant Max Current(Arms) | 30 | 36 | 50 | |
Rated Speed(rpm) | 3000 | 3000 | 2500 | |
MaxSpeed(rpm) | 6000 | 6000 | 4000 | |
Torque Parameter(Nm/Arms) | 0.12 | 0.12 | 0.16 | |
Rotor inertia 10-4kg.m² | 0.593 | 0.766 | 1.27 | |
Back EMF coefficient(Vrims/rad/s) | 7 | 7 | 10 | |
Resistance(Ω) | 0.16 | 0.12 | 0.09 | |
Inductance(mH) | 0.2 | 0.144 | 0.1 | |
Pole-pairs number(2P) | 10 | 10 | 10 | |
Weight(kg) | 0.306 | 0.414 | 0.736 | |
Motor height(mm) | L1 | 10.5 | 15 | 28 |
L2 | 11 | 15.5 | 28.5 | |
L3 | 19.6 | 23.9 | 37.7 |
Drawing
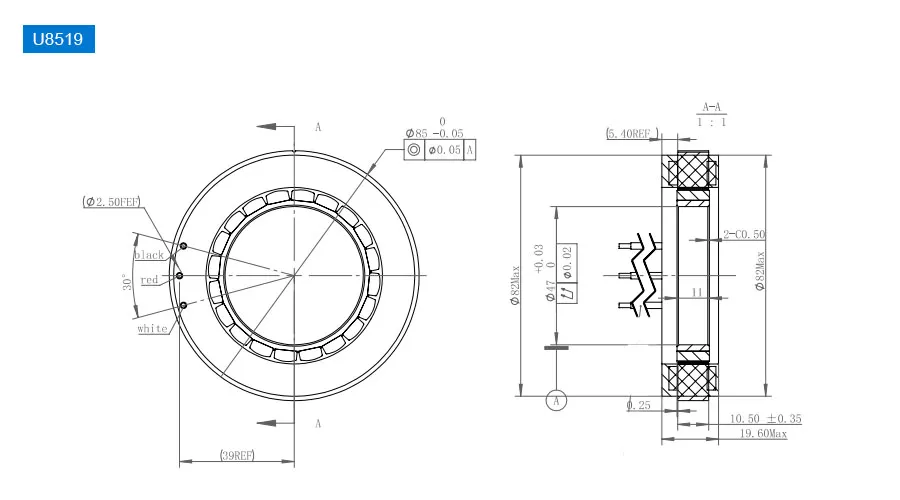
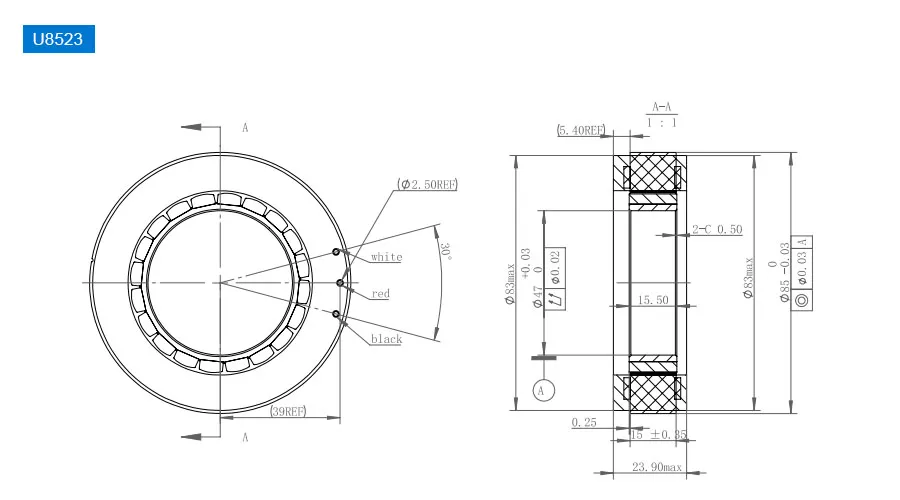
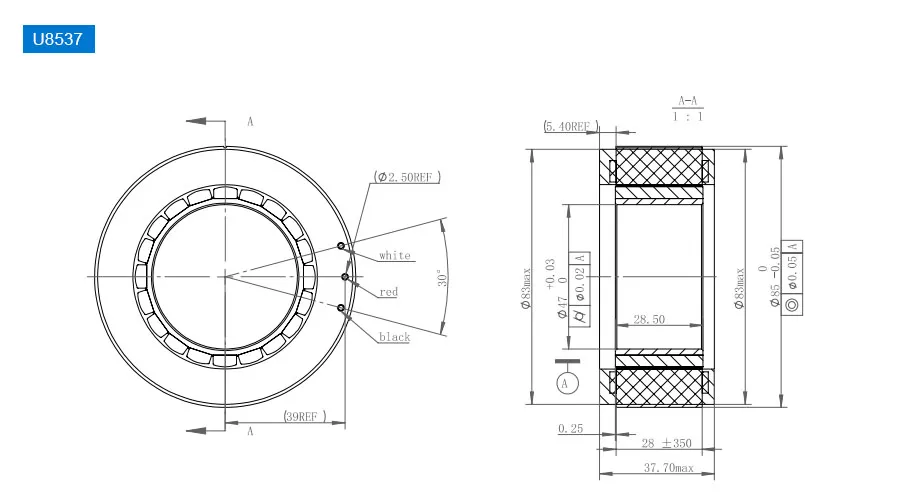
Case studies (Customized frameless motors developed with our clients)
Additional Info
Features & Benefits:
• High torque from 1.21 Nm to 2.69 Nm
• High speeds up to 6,000 RPM
• Superior performance – high stiffness and better response
• High reliability – no mechanical transmission devices like couplings, flanges
• Compact design – minimizes product size
• Low cogging - unique magnetic circuit design decreases cogging
Applications:
• Automotive
• Machine tool
• Material handling
• Packaging
• Robotics
• Semiconductor
When to Use:
• Substantial cost savings
• Decreased mechanical complexity
• Enhanced flexibility in design
• Exceptional performance in a compact space
• Improved dynamic response
• Minimum motor size in each application
• Low cogging for smooth operation
• Low inertia allows for quicker acceleration
Download
U8519 Torque Motor Catalog.pdf
OD: 85mm|Height: 19.3mm
U8523 Torque Motor Catalog.pdf
OD: 85mm|Height: 23.8mm
U8537 Torque Motor Catalog.pdf
OD: 85mm|Height: 37.4mm
U85 Series Frameless Brushless Motor Catalog.pdf
OD: 85mm|Height: 19.3~23.8~37.4mm optional
OD: 85mm|Height: 19.3mm
OD: 85mm|Height: 23.8mm
OD: 85mm|Height: 37.4mm
-
-
-
-
Frequently bought together - Magnetic encoders
Direct drives need high-quality position signals to ensure optimal performance. Perfect measuring signals can enhance the surface quality of machined workpieces, reduce the machine frame's vibrations, minimize velocity-dependent motor noise, and prevent excessive heat generation in the motor.
Mosrac recommends using a magnetic encoder to enhance the accuracy, speed stability, and thermal behavior of direct drive axes. Because there is no mechanical transmission between the encoder and the feed unit, the position signals are not susceptible to inaccuracies or delays.
Custom combinations are available on request and contact us.
Previous