Specification
Main Parameters | U16025 | U16035 | U16060 | |
Voltage(VDC) | 48 | 48 | 48 | |
Rated Output(W) | 471.6 | 471.6 | 670.72 | |
Rated torque(Nm) | 9 | 15 | 32 | |
Instant Max Torque(Nm) | 20 | 32 | 66 | |
Rated Current(Arms) | 15 | 17 | 20 | |
Instant Max Current(Arms) | 35 | 38 | 45 | |
Rated Speed(rpm) | 500 | 300 | 200 | |
MaxSpeed(rpm) | 800 | 600 | 400 | |
Torque constant (Nm/Arms) | 0.60 | 0.88 | 1.6 | |
Rotor inertia 10-4kg.m² | 9.2 | 14 | 26 | |
Back EMF coefficient(V/Krpm) | 42 | 61 | 84 | |
Resistance(Ω) | 0.18 | 0.2 | 0.16 | |
Inductance(mH) | 0.35 | 0.44 | 0.35 | |
Pole-pairs number(2P) | 13 | 13 | 13 | |
Weight(kg) | 1.1 | 1.6 | 3.3 | |
Length L(mm) | L1 | 16.6 | 24.6 | 48.6 |
L2 | 16 | 24 | 48 | |
L3 | 25.9 | 35.9 | 60.9 |
Main Parameters | U16025 | U16035 | U16060 | |
Voltage(VDC) | 220 | 220 | 220 | |
Rated Output(W) | 1886.4 | 1257.6 | 2012.16 | |
Rated torque(Nm) | 9 | 15 | 32 | |
Instant Max Torque(Nm) | 20 | 32 | 66 | |
Rated Current(Arms) | 10 | 10 | 10 | |
Instant Max Current(Arms) | 25 | 25 | 25 | |
Rated Speed(rpm) | 2000 | 800 | 600 | |
MaxSpeed(rpm) | 3000 | 1500 | 1000 | |
Torque constant (Nm/Arms) | 0.90 | 1.50 | 3.20 | |
Rotor inertia 10-4kg.m² | 9.2 | 14 | 26 | |
Back EMF coefficient(V/Krpm) | 70 | 100 | 176 | |
Resistance(Ω) | 0.5 | 0.55 | 0.87 | |
Inductance(mH) | 1 | 1.2 | 1.79 | |
Pole-pairs number(2P) | 13 | 13 | 13 | |
Weight(kg) | 1.1 | 1.6 | 3.3 | |
Length L(mm) | L1 | 15.5 | 23 | 47 |
L2 | 16.60 | 24.60 | 48.60 | |
L3 | 25.90 | 35.90 | 60.90 |
Drawing
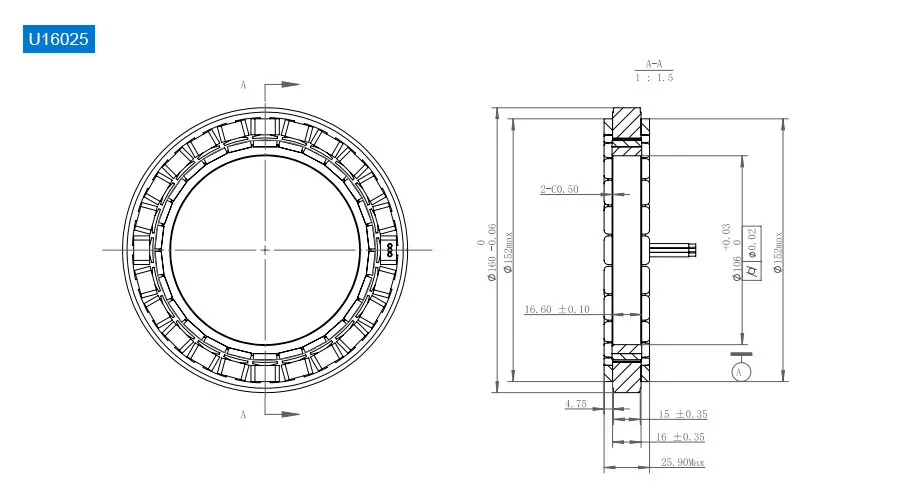
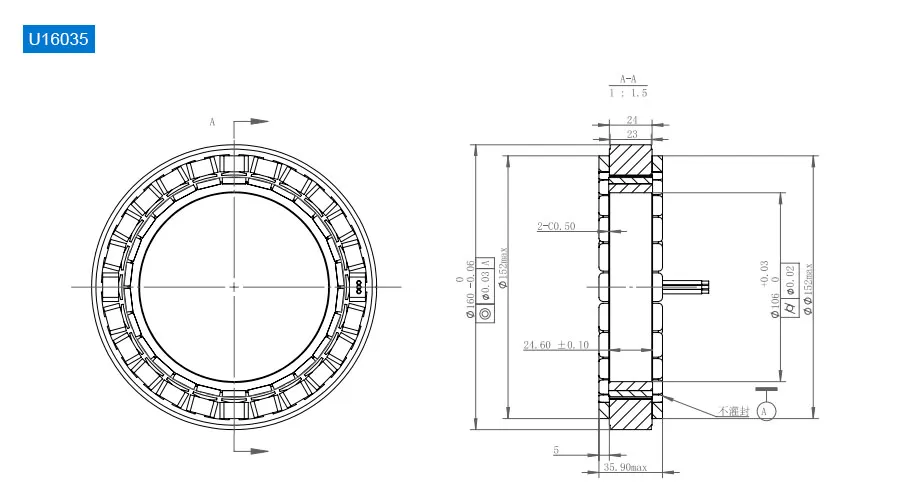
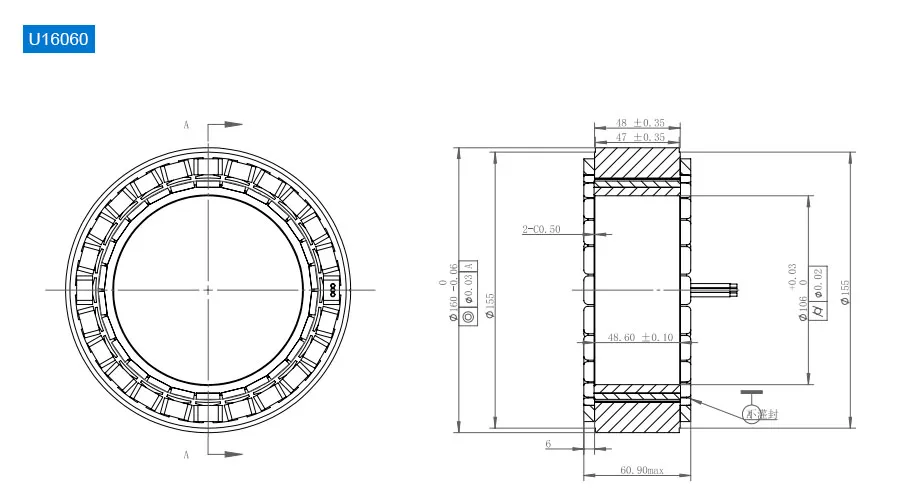
Case studies (Customized frameless motors developed with our clients)
Additional Info
Mosrac’s U-Series frameless stator-rotor kits, developed through integrated engineering, provide industry-leading torque density, unsurpassed precision, and excellent overload capacity in a highly compact space. Customizable options, including alternative voltage levels and tailored torque-speed characteristics, are available to meet specific needs.
With development expertise, engineering support, and comprehensive documentation, the Mosrac R&D team ensures seamless implementation of solutions optimized for size, thermal performance, and other unique requirements.
Features:
▪︎ Frame size 160 mm OD
▪︎ Max speeds up to 800 rpm
▪︎ Pole-pairs number (2P): 13 or custom
▪︎ 48 VDC Rated Voltage
▪︎ 35-45 Arms Rated Current
▪︎ Continuous torque range from 9 N-m to 32 N-m
▪︎ Peak torque range from 20 N-m to 66 N-m
▪︎ CE, RoHS, REACH Compliant
▪︎ Standard windings to match special speed and torque performance requirements
▪︎ Optional Hall sensors or encoders as rotor position feedback devices
▪︎ Frameless models use the load’s shaft, bearings, Hall sensors, and additional position feedback devices such as encoders.
Benefits:
One of the latest next-generation frameless motors is hollow-shaft U160 series stator-rotor kits,
which offer market-leading torque density and maximum design freedom for structurally integrated drive engineering.
Our frameless BLDC motor range is available in various sizes and rated torque.
▪︎ Frameless construction provides a high level of design flexibility
▪︎ Offers excellent torque density at a competitive price
▪︎ Features hollow-shaft capability
▪︎ Lightweight and compact design
▪︎ Operates on low voltage, ranging from 12V to 48V
▪︎ High torque density and dynamic performance are achieved through an excellent copper fill factor
▪︎ Reduced thermal losses due to concentrated coils
▪︎ Drive system design is optimized for weight and installation space based on load profile analysis
▪︎ Provides excellent dynamic control and precision
▪︎ Ideal for a diverse range of applications
Applications:
▪︎ Machine tool
▪︎ Packaging
▪︎ Robotics
▪︎ Semiconductor
▪︎ Automotive
When to Use:
▪︎ Substantial cost savings
▪︎ Decreased mechanical complexity
▪︎ Enhanced flexibility in design
▪︎ Exceptional performance in a compact space
▪︎ Improved dynamic response
▪︎ Minimum motor size in each application
▪︎ Low cogging for smooth operation
▪︎ Low inertia allows for quicker acceleration
Download
U16025 Torque Motor Catalog.pdf
OD: 160mm|Height: 25.9mm
U16035 Torque Motor Catalog.pdf
OD: 160mm|Height: 35.9mm
U16060 Torque Motor Catalog.pdf
OD: 160mm|Height: 60.9mm
U160 Series Frameless Brushless DC Motor Catalog.pdf
OD: 160mm|Height: 25.9~35.9~60.9mm optional
OD: 160mm|Height: 25.9mm
OD: 160mm|Height: 35.9mm
OD: 160mm|Height: 60.9mm
-
-
-
-
Frequently bought together - Magnetic encoders
Direct drives need high-quality position signals to ensure optimal performance. Perfect measuring signals can enhance the surface quality of machined workpieces, reduce the machine frame's vibrations, minimize velocity-dependent motor noise, and prevent excessive heat generation in the motor.
Mosrac recommends using a magnetic encoder to enhance the accuracy, speed stability, and thermal behavior of direct drive axes. Because there is no mechanical transmission between the encoder and the feed unit, the position signals are not susceptible to inaccuracies or delays.
Custom combinations are available on request and contact us.
Previous